Скенирајући електронски микроскоп је коришћен за посматрање лома услед замора и анализу механизма лома; у исто време, извршено је испитивање замора савијањем центрифугирањем на разугљиченим узорцима на различитим температурама да би се упоредио век замора испитиваног челика са и без разугљиковања и да би се анализирао ефекат разугљичења на перформансе замора испитиваног челика. Резултати показују да, услед истовременог постојања оксидације и декарбонизације у процесу загревања, интеракција између њих, која резултира дебљином потпуно разугљиченог слоја са порастом температуре, показује тренд повећања, а затим опадања. дебљина потпуно разугљиченог слоја достиже максималну вредност од 120 μм на 750 ℃, а дебљина потпуно разугљиченог слоја достиже минималну вредност од 20 μм на 850 ℃, а граница замора испитног челика је око 760 МПа, и извор заморних пукотина у испитиваном челику су углавном неметалне инклузије Ал2О3; Понашање при разугљиковању у великој мери смањује век трајања тест челика, утичући на перформансе замора испитног челика, што је дебљи слој за разугљичење, то је нижи век замора. Да би се смањио утицај слоја за декарбонизацију на перформансе замора испитиваног челика, оптимална температура термичке обраде испитног челика треба да буде подешена на 850 ℃.
Опрема је важна компонента аутомобила,због рада при великој брзини, мрежасти део површине зупчаника мора имати високу чврстоћу и отпорност на хабање, а корен зуба мора имати добре перформансе замора при савијању услед сталног понављаног оптерећења, како би се избегле пукотине које доводе до материјала прелом. Истраживања показују да је разугљичење важан фактор који утиче на перформансе замора металних материјала савијањем при центрифугирању, а перформансе замора савијањем центрифугирањем су важан показатељ квалитета производа, тако да је неопходно проучити понашање разугљиковања и перформансе замора центрифугирања испитиваног материјала.
У овом раду, пећ за термичку обраду на тесту разугљичења површине 20ЦрМнТи челика зупчаника, анализира различите температуре загревања на тестној дубини слоја декарбонизације челика променљивог закона; користећи КБВП-6000Ј једноставну машину за испитивање замора снопа на тесту замора при ротационом савијању тест челика, одређивање перформанси тестног челика замора, и истовремено анализирати утицај декарбонизације на перформансе замора испитног челика за стварну производњу да би се побољшала производног процеса, побољшати квалитет производа и пружити разумну референцу. Перформансе замора челика за испитивање се одређују помоћу машине за испитивање замора савијања савијањем.
1. Испитни материјали и методе
Испитни материјал за јединицу која обезбеђује зупчасти челик од 20ЦрМнТи, главни хемијски састав као што је приказано у табели 1. Тест декарбонизације: тест материјал се обрађује у цилиндрични узорак Ф8 мм × 12 мм, површина треба да буде светла без мрља. Пећ за термичку обраду је загрејана на 675 ℃, 700 ℃, 725 ℃, 750 ℃, 800 ℃, 850 ℃, 900 ℃, 950 ℃, 1.000 ℃, а затим је држана на температури од 1 х у просторији. Након термичке обраде узорка постављањем, брушењем и полирањем, са 4% ерозије раствора алкохола азотне киселине, примена металуршке микроскопије за посматрање слоја за разугљичење тестног челика, мерење дубине разугљичног слоја на различитим температурама. Испитивање замора савијањем савијањем: испитни материјал у складу са захтевима обраде две групе узорака замора савијањем савијањем, прва група не спроводи тест разугљичења, друга група теста разугљичења на различитим температурама. Користећи машину за испитивање замора савијањем, две групе испитног челика за испитивање замора при савијању, одређивање границе замора две групе испитиваног челика, поређење века трајања замора две групе тест челика, употреба скенирања посматрање лома услед замора електронским микроскопом, анализира разлоге лома узорка, да би се истражио ефекат разугљиковања на својства замора испитиваног челика.
Табела 1 Хемијски састав (масени удео) испитиваног челика теж.%
Утицај температуре загревања на декарбонизацију
Морфологија организације разугљичења при различитим температурама загревања приказана је на слици 1. Као што се може видети са слике, када је температура 675 ℃, на површини узорка се не појављује разугљични слој; када температура порасте на 700 ℃, почео је да се појављује слој за разугљичење површине узорка, за танки слој за разугљичење ферита; са порастом температуре на 725 ℃, дебљина слоја декарбонизације површине узорка значајно се повећала; 750 ℃ Дебљина слоја декарбонизације достиже своју максималну вредност, у овом тренутку феритно зрно је јасније, грубље; када температура порасте на 800 ℃, дебљина слоја за разугљичење је почела значајно да опада, његова дебљина је пала на половину од 750 ℃; када температура настави да расте на 850 ℃ и дебљина разугљиковања је приказана на слици 1. 800 ℃, пуна дебљина слоја за разугљичење је почела значајно да опада, његова дебљина је пала на 750 ℃ када је половина; када температура настави да расте на 850 ℃ и више, дебљина слоја за потпуно разугљичење тестног челика наставља да се смањује, половина дебљине слоја за разугљичење је почела постепено да се повећава све док морфологија потпуног слоја за разугљичење не нестане, а половина слоја за разугљичење се постепено чисти. Види се да је дебљина потпуно разугљиченог слоја са порастом температуре прво повећана, а затим смањена, разлог за ову појаву је због тога што се узорак у процесу загревања истовремено понаша оксидационо и декарбонизовано, само када стопа разугљичења је већа од брзине оксидације појавиће се феномен разугљичења. На почетку загревања, дебљина потпуно разугљиченог слоја се постепено повећава са порастом температуре све док дебљина потпуно разугљиченог слоја не достигне максималну вредност, у овом тренутку да би се наставило да повећава температуру, брзина оксидације узорка је већа од стопа разугљиковања, која инхибира повећање потпуно разугљиченог слоја, што резултира опадајућим трендом. Може се видети да је, у опсегу од 675 ~950 ℃, вредност дебљине потпуно разугљиченог слоја на 750 ℃ највећа, а вредност дебљине потпуно разугљиченог слоја на 850 ℃ најмања, стога се препоручује да температура загревања испитног челика буде 850℃.
Слика 1 Хистоморфологија разугљиченог слоја тест челика држаног на различитим температурама загревања 1х
У поређењу са полу-разугљиченим слојем, дебљина потпуно декарбозираног слоја има озбиљнији негативан утицај на својства материјала, то ће у великој мери смањити механичка својства материјала, као што је смањење чврстоће, тврдоће, отпорности на хабање и границе замора , итд., а такође повећавају осетљивост на пукотине, утичући на квалитет заваривања и тако даље. Због тога је контрола дебљине потпуно декарбозираног слоја од великог значаја за побољшање перформанси производа. На слици 2 приказана је крива варијације дебљине потпуно разугљиченог слоја са температуром, која јасније приказује варијацију дебљине потпуно разугљиченог слоја. Са слике се може видети да је дебљина потпуно разугљиченог слоја само око 34 μм на 700 ℃; са порастом температуре на 725 ℃, дебљина потпуно разугљиченог слоја значајно се повећава на 86 μм, што је више од два пута дебљине потпуно разугљиченог слоја на 700 ℃; када се температура подигне на 750 ℃, дебљина потпуно разугљиченог слоја Када температура порасте на 750 ℃, дебљина потпуно разугљиченог слоја достиже максималну вредност од 120 μм; како температура наставља да расте, дебљина потпуно декарбозираног слоја почиње нагло да опада, на 70 μм на 800 ℃, а затим на минималну вредност од око 20 μм на 850 ℃.
Слика 2 Дебљина потпуно разугљиченог слоја на различитим температурама
Утицај декарбонизације на перформансе замора при савијању центрифуге
У циљу проучавања утицаја разугљиковања на својства замора опружног челика, спроведене су две групе испитивања замора савијањем центрифугирањем, прва група је била испитивање замора директно без разугљичења, а друга група је била испитивање замора након разугљичења при истом напрезању. ниво (810 МПа), а процес декарбонизације је држан на 700-850 ℃ током 1 х. Прва група узорака приказана је у табели 2, која представља заморни век челика за опруге.
Век трајања прве групе узорака на замор приказан је у табели 2. Као што се може видети из табеле 2, без разугљиковања, испитни челик је био подвргнут само 107 циклуса на 810 МПа и није дошло до лома; када је ниво напрезања прешао 830 МПа, неки од примерака су почели да се ломе; када је ниво напрезања прешао 850 МПа, сви узорци замора су били поломљени.
Табела 2 Век трајања замора под различитим нивоима напрезања (без декарбонизације)
За одређивање границе замора користи се групна метода за одређивање границе замора испитиваног челика, а након статистичке анализе података, граница замора испитног челика је око 760 МПа; да би се карактерисао век замора испитиваног челика под различитим напонима, СН крива је уцртана, као што је приказано на слици 3. Као што се може видети са слике 3, различити нивои напона одговарају различитом веку замора, када је век замора од 7 , што одговара броју циклуса за 107, што значи да је узорак у овим условима кроз стање, одговарајућа вредност напона се може апроксимирати као вредност заморне чврстоће, односно 760 МПа. Може се видети да је С - Н крива важна за одређивање заморног века материјала има важну референтну вредност.
Слика 3 СН крива експерименталног испитивања замора челика ротирајућим савијањем
Заморни век друге групе узорака приказан је у табели 3. Као што се види из табеле 3, након што се испитни челик разугљичи на различитим температурама, број циклуса је очигледно смањен, и они су више од 107, а све заморни узорци су поломљени, а животни век је значајно смањен. У комбинацији са горњом дебљином разугљиченог слоја са кривом промене температуре може се видети, 750 ℃ дебљина разугљиченог слоја је највећа, што одговара најнижој вредности века трајања. Дебљина разугљиченог слоја од 850 ℃ је најмања, што одговара вредности века трајања замора је релативно висока. Може се видети да понашање разугљичења у великој мери смањује перформансе материјала при замору, а што је дебљи разугљичени слој, то је нижи век трајања замора.
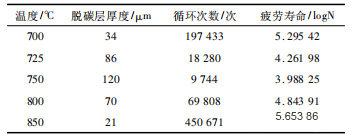
Табела 3 Век трајања замора при различитим температурама декарбонизације (560 МПа)
Морфологија лома узорка од замора посматрана је скенирајућим електронским микроскопом, као што је приказано на слици 4. На слици 4(а) за подручје извора прслине, на слици се може видети очигледан лук замора, према луку замора да би се пронашао извор од замора, може се видети, извор пукотина за неметалне инклузије „рибљег ока“, инклузије при концентрацији напрезања која се лако изазива, што доводи до заморних прслина; На слици 4(б) за морфологију подручја проширења пукотине, могу се видети очигледне траке замора, дистрибуција је налик на реку, припада квази-дисоцијативном лому, са пукотинама које се шире, што на крају доводи до лома. Слика 4(б) приказује морфологију подручја ширења пукотине, виде се очигледне пруге замора, у облику речне дистрибуције, која припада квази-дисоцијативном лому, и уз континуирано ширење пукотина, што на крају доводи до лома. .
Анализа лома замора
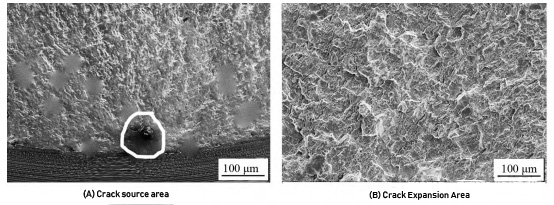
Сл.4 СЕМ морфологија површине лома од замора експерименталног челика
Да би се одредио тип инклузија на Сл. 4, извршена је анализа састава енергетског спектра, а резултати су приказани на Сл. 5. Може се видети да су неметалне инклузије углавном Ал2О3 инклузије, што указује да су инклузије су главни извор пукотина узрокованих пуцањем инклузија.
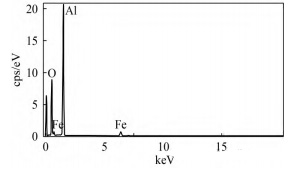
Слика 5 Енергетска спектроскопија неметалних инклузија
Закључи
(1) Постављање температуре грејања на 850 ℃ ће минимизирати дебљину разугљиченог слоја како би се смањио ефекат на перформансе замора.
(2) Граница замора тестног челика савијањем центрифуге је 760 МПа.
(3) Испитивање пуцања челика у неметалним инклузијама, углавном мешавином Ал2О3.
(4) декарбонизација озбиљно смањује век замора испитног челика, што је дебљи слој за разугљичење, то је нижи век замора.
Време поста: 21.06.2024